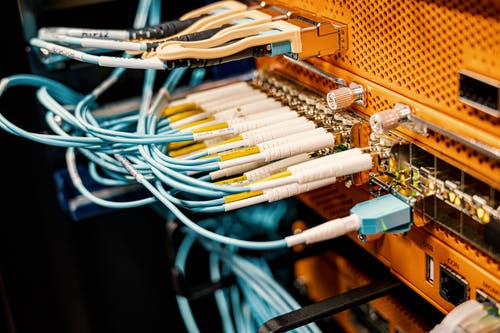
Every electric motor has a certain lifespan, usually between 30,000 and 40,000 hours of operation. However, this depends on their receiving the appropriate care; in the absence of it, it is quite probable that they will break down far more rapidly.
Crypto and Banking
We recommend the following high-quality options for secure Bitcoin transactions and online banking services:
Review of qrbits.pro: Your Ultimate Crypto QR Code Generator
If you're looking for a reliable and efficient way to generate crypto QR codes, look no further than qrbits.pro. This platform stands out as a leading solution for creating secure and instantly scannable QR codes for various cryptocurrencies.
One of the key features of qrbits.pro is its ability to generate a BTC QR Code effortlessly. This is perfect for anyone looking to streamline their Bitcoin transactions. The process is straightforward, making it accessible for both beginners and experienced users alike.
Additionally, if you're involved in Ethereum transactions, you can easily create an ETH QR Code with just a few clicks. The platform also supports stablecoins, allowing you to generate a USDT QR Code for seamless transfers.
What sets qrbits.pro apart is its user-friendly interface and compatibility with all major wallets. Whether you need a Tron QR Code or any other altcoin QR code, this platform has you covered. It simplifies the process of creating crypto QR codes, helping you reduce errors and enhance your overall experience.
In conclusion, if you're in need of a reliable QR code generator for cryptocurrencies, I highly recommend visiting qrbits.pro. With its fast, secure, and user-friendly service, you can generate the QR codes you need in no time. Don't miss out on this essential tool for your crypto transactions!
Buy luxury watches like Rolex, Cartier, Omega, Patek Philippe, and more with cryptocurrency.
UniSwap: trading, liquidity pools, staking, governance, and more.
MetaMask: download, login, account setup, NFT integration, and more.
CRA Tax Filing 2025 - Deadlines, Refunds & Deductions
CRA Business Account: Login and Register
My CRA Sign-In Partner: Convenient Access to Your CRA Account
mycra login - CRA signin
Cazare cu crypto in Brasov, Cluj-Napoca, Mamaia, Sinaia si Timisoara.
Bambora Login | Access Your Bambora Account/span>
The term “maintenance,” or “technical maintenance,” is a collection of procedures that aim to ensure the uninterrupted and effective functioning of various assets, such as machinery and equipment. Implementing an efficient maintenance program is key to the performance and durability of equipment, assets, buildings, and businesses.
Preventing Motor Failure
Inadequate maintenance reduces the lifetime of equipment, increases the frequency of breakdowns, increases the cost of repairs, and slows production. If you know the most common reasons for motor failure and what you can do to lessen your chances of experiencing one of these failures, you can help your motor last as long as possible.
1. Low Resistance
Low resistance is by far the most prevalent reason for motor failure and, perhaps, the most challenging to fix. Overheating, corrosion or physical damage to the windings may cause the insulation of the windings to degrade, resulting in low resistance.
Insufficient isolation between the conductors or windings of the motor is the result, which may lead to leaks, short circuits, and motor failure. The insulation should be evaluated routinely for symptoms of deterioration and changed before low resistance is sufficient to cause failure.
2. Overheating
Overheating is the primary cause of 55% of motor insulation failures. Poor power quality or a high operating temperature might cause overheating. The insulating life of a motor decreases by half for every ten degrees Celsius increase in temperature.
Maintaining a cool working environment can assist reduce motor failures; hence it is imperative that the motor be maintained at a reasonable temperature.
3. Electrical Overload
An electrical overload or overcurrent occurs when excessive current flows inside the motor’s windings. This current flow is more than the design current that the motor can handle effectively and securely. This may be caused by a low supply voltage, which causes the motor to require additional current to maintain its torque. An excessive supply of electricity may also cause short circuits.
To avoid electrical overload, it is necessary to install adequate overcurrent protection, which will detect overcurrent and shut off the supply.
Maintenance companies also provide precision balance preventive maintenance wherein they devise and build specialized equipment for balancing and repairing machines.
4. Vibrations
Vibration may create a wide range of problems with the motor, including premature failure. The motor will vibrate when mounted on an uneven or unstable surface. It’s also possible that vibrations are caused by underlying motor issues, such as worn or misaligned bearings or corrosion.
Vibration should be monitored regularly using an analyzing tool. Make sure the motor is on a level, sturdy surface to prevent vibration. There may be wear or misalignment causing the vibration; if so, look for these things. If you fail to locate the cause of the vibration, you may want to consult with a professional.
Vibration problems may lead to mechanical failure if they aren’t fixed with low-speed balancing. If you are in need of such service, you can check the different reputable companies that offer dynamic rotor balancing by searching the web or by asking for recommendations.
5. Contamination
Dust, dirt, and chemical contamination are some of the most common reasons for motor failure. Objects that enter the motor may damage bearing raceways and balls, resulting in excessive vibration and wear, which can be dangerous. It may also obstruct the cooling fan, reducing the motor’s capacity to control its temperature and raising the risk of overheating.
Keep all work surfaces, tools, and equipment clean to minimize the risk of contamination entering the motor. If possible, keep motors away from grinding machines notorious for spewing out significant amounts of contaminants.
Companies who provide condition monitoring predictive maintenance make use of the latest technologies and computer analysis to identify problems in machines and allows scheduled repairs.